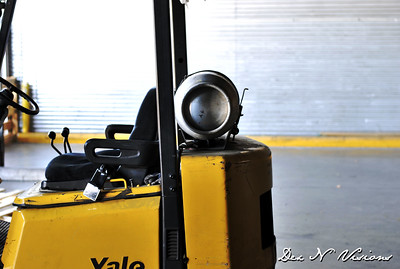
A forklift propane regulator is a device that is attached to the tank of a forklift in order to regulate the flow of propane to the engine. It is responsible for ensuring that the correct amount of propane is delivered to the engine, and it also prevents the engine from being overloaded with propane.
It is a device that controls the pressure of propane in a tank or other container. It is composed of a valve and a gauge. The valve is used to regulate the flow of propane, and the gauge is used to measure the pressure of the propane. The propane regulator is used to keep the pressure of the propane at a safe level.
Propane is liquid state when it is stored inside a compressed cylinder which is the tank. When the propane is released, it turns into gas, flowing into the gas line and into the fuel filter to clean the gas from any contaminants and to its next destination in the fuel system: the regulator.
It works together with the solenoid so that the gas flows and stops flowing depending on the signal from the ECU. The solenoid acts as an access door for the propane. It opens when the engine ignition and starter are both turned on. The ECU controls the solenoid and gives instructions to it. When the ECU determines that the solenoid has been supplied with current, the solenoid then opens and the flow of the propane enters into the regulator.
When the propane reaches the regulator, it turns into gas vapor. This vapor has pressure. The pressure must be precise so that proper combustion can take place inside the engine. Depending on the fuel injector, the pressure ranges between 3-5.5 PSI.
The vaporized propane then travels to one of the important parts of the fuel system: the mixer. The mixer, as its name implies, mixes the gas with air. When air and gas are mixed, they go to the throttle body. The throttle body then gives or shuts off the flow of gas/air mix into the fuel injector.
This gas/air mixture then travels to the intake manifold for combustion. The forklift’s fuel system works the same as the car’s fuel system.
The Role of the Pressure Regulator in Maintaining Pressure Levels
- it reduces the high tank pressure to a lower, usable level for the engine.
- It maintains a constant outlet pressure, regardless of variations in the tank pressure or the rate of gas consumption by the engine.
How the Diaphragm Responds to Changes in Gas Flow and Pressure
- The diaphragm assembly, which includes a flexible diaphragm and springs, reacts to the downstream pressure of the gas.
- If the downstream pressure drops (as the engine demands more fuel), the diaphragm moves to open the valve further, allowing more propane to flow.
- Conversely, if the downstream pressure rises, the diaphragm compresses the spring to reduce the gas flow.
The Function of the Pressure Relief Valve in Preventing Over-Pressurization
- The pressure relief valve is set to open at a specified pressure limit to prevent the system from reaching dangerous pressure levels.
- Should the regulator malfunction or if there is an abnormal pressure increase, the valve releases propane into the atmosphere to defuse the potential for damage or explosion.
The Importance of the Flow Control Valve in Regulating Propane Delivery
- The flow control valve fine-tunes the amount of gas sent to the engine, ensuring the correct air-to-fuel ratio for efficient combustion.
- It adjusts the flow based on the engine’s power needs, which can vary depending on the forklift’s load and operating conditions.
The Servo Operation and Its Impact on Regulator Performance
- The servo operation mechanism enhances the sensitivity and responsiveness of the regulator.
- It uses engine vacuum and pressure feedback to make precise adjustments to the diaphragm position, thus stabilizing the gas flow rate in real-time.
The Lock-off Valve’s Role in Safety and Operation
- The lock-off valve is a fail-safe that cuts off the propane supply when the engine is stopped or in the event of a malfunction.
- It ensures that propane does not flow unless the engine is in operation, preventing build-up of fuel within the engine and reducing the risk of fire or explosion when the engine is off.
Main Components of a Forklift Propane Regulator
Pressure Regulator Valve
- The pressure valve is a critical component designed to receive propane from the tank at high pressure and reduce it to a consistent, lower pressure suitable for the forklift’s engine combustion process.
- It ensures the engine receives a steady flow of gas at a pressure it can handle, which is essential for smooth operation and to prevent damage to the engine.
Diaphragm Assembly
- The diaphragm assembly is a flexible membrane that responds to changes in downstream pressure and acts to adjust the flow of propane accordingly.
- It operates in conjunction with springs and other mechanical parts to regulate the pressure of the gas being delivered to the engine, ensuring that the engine runs efficiently.
Pressure Relief Valve
- This safety feature is designed to release excess pressure if the gas pressure within the system becomes too high, which can occur due to environmental factors or system malfunctions.
- The pressure relief valve helps to prevent potential hazards by ensuring that the pressure within the propane system stays within safe operating limits.
Flow Control Valve
- The flow control valve works alongside the regulator to control the rate at which propane is delivered to the engine.
- Adjusting the size of the opening through which propane passes, helps to maintain the correct fuel-to-air ratio for optimal engine performance.
Servo Operation Mechanism
- The servo operation mechanism assists in the precise control of the gas flow by responding to minute changes in engine demand.
- It uses feedback from the engine’s operations to adjust the position of the diaphragm assembly and the flow control valve dynamically, ensuring responsive control over the propane delivery.
Lock-off Valve
- The lock-off valve is a safety component that stops the flow of propane completely when the forklift’s engine is not running or when there is a need to shut off the fuel supply abruptly.
- This valve is typically engaged when the ignition is turned off, during maintenance, or in an emergency situation to prevent the escape of gas.
Each of these components plays a vital role in the functioning of a forklift propane regulator, ensuring that the propane is delivered safely and efficiently from the tank to the forklift’s engine. Proper maintenance and regular inspections of these components are crucial for the safe and effective operation of propane-powered forklifts.
The Role of the Regulator in Forklift Performance
The role of the propane regulator in forklift performance is critical, as it directly influences the efficiency and reliability of the engine. Here’s how:
A. Impact on Fuel Efficiency
- Optimal Air-Fuel Mixture: The component ensures that the propane is at the correct pressure to mix adequately with air, providing an optimal air-fuel mixture for combustion.
- Consistent Fuel Supply: It maintains a consistent fuel supply to the engine, which is crucial for efficient fuel usage.
- Prevent Fuel Wastage: A properly functioning unit avoids excess consumption or wastage of fuel, contributing to better fuel economy.
B. Impact on Forklift Engine Performance
- Engine Power: The unit influences the engine’s ability to produce power. Inconsistent or incorrect pressure can lead to poor engine performance.
- Engine Lifespan: By ensuring a clean and correct fuel flow, this part of the forklift can also affect the longevity of the engine, preventing damage due to lean (too much air) or rich (too much fuel) running conditions.
- Smooth Operation: The forklift’s operations, such as lifting and moving loads, require smooth and responsive engine performance, which is facilitated by the proper functioning of the regulator.
C. Consequences of its Failure
- Increased Fuel Consumption: A failing unit may cause the engine to consume more fuel than necessary, leading to increased operational costs.
- Reduced Engine Efficiency: If the component does not provide the right fuel pressure, the engine may not run efficiently, resulting in decreased performance and potential for stalling or power loss during critical tasks.
- Engine Damage: An improper mixture or fuel delivery may cause internal engine damage over time, such as burned valves or damaged pistons due to lean or rich running conditions.
- Safety Hazards: Its failure could lead to propane leaks, which are a significant safety hazard in the workplace. In addition to the risk of fire or explosion, there’s also the potential for asphyxiation in poorly ventilated areas.
- Downtime and Repairs: Equipment failure due to some issues can lead to increased downtime, interrupting workflow and requiring potentially costly repairs.
Proper maintenance, timely troubleshooting, and regular inspections are essential practices to ensure that the forklift performs efficiently, safely, and reliably. Keeping it in good working condition helps prevent operational disruptions and extends the service life of the forklift.
What are the different types of propane regulators?
They come in various designs, each suited to specific types of engines and operational requirements. Here are some common types used in forklifts:
- Single-Stage: These regulators reduce the tank pressure to the required pressure level in a single step. They are simple and often used in systems where precise control of the output pressure is not critical.
- Two-Stage: These are more common in forklift applications. They reduce the tank pressure in two steps, which provides a more consistent output pressure. The first stage cuts down the tank pressure to a preset intermediate level, and the second stage further reduces it to the required working pressure. This type is better for applications that need steady pressure despite fluctuations in tank pressure or flow demand.
- Integral Twin Stage: These combine both stages of pressure reduction into a single compact unit. They are designed to provide a constant delivery pressure with varying flow rates and inlet pressures, which is ideal for forklift operations that demand consistent performance.
- Automatic Changeover: These are designed for systems with dual propane tanks. They automatically switch from an empty tank to a full one, ensuring a continuous supply of propane without manual intervention.
- Adjustable High-Pressure: While not typically used on standard forklifts, these are available for specialized applications. They allow for manual adjustment of the output pressure for tasks that require varying pressures.
- Vaporizers-Regulators: Propane can be stored as a liquid and needs to be converted to a vapor before use in an engine. Some forklift systems use a vaporizer-regulator which not only reduces the pressure but also ensures the propane is in a gaseous state when it reaches the engine.
Each type is designed to meet specific demands in terms of flow rate, pressure stability, and environmental conditions. The choice will depend on factors such as forklift engine type, operating temperatures, and the nature of the work being performed.
It’s important to select the appropriate type for the specific make and model of the forklift, as well as the operating conditions it will encounter. Incorrect type selection can lead to performance issues, increased wear and tear on the engine, or even safety hazards. Regular maintenance and checks are also crucial to ensure that the regulator functions as intended over time.
How can you tell if your unit is working properly?
Determining if it is working properly involves several checks and observations specific to the operational context of a forklift:
- Engine Start-Up: The forklift should start without excessive cranking. Difficulty starting the engine might indicate that the regulator is not supplying the correct amount of propane.
- Engine Performance: Once the forklift engine is running, it should operate smoothly. If the engine runs rough, stalls frequently, or has fluctuations in power, this could be a sign that the unit is not maintaining the proper propane flow.
- Fuel Consumption: Monitor the fuel usage of the forklift. A regulator that is not functioning properly may cause the engine to consume propane too quickly or inefficiently.
- Visual Inspection: Check the unit for signs of damage, corrosion, or excessive wear. All connections should be secure without any signs of damage or leaks.
- Leak Testing: Perform a leak test by applying a soapy water solution to the regulator and hose connections. Look for bubbles that indicate escaping gas.
- Check Flame Color (if accessible): A blue flame in the forklift’s engine is normal, while a yellow or orange flame can indicate incomplete combustion, often due to incorrect gas pressure or flow, which could be caused by a faulty unit.
- Pressure Gauges: If the forklift has a pressure gauge installed, it should indicate steady pressure levels that match the specifications for the forklift. Fluctuating pressures or pressures that are too high or too low can indicate a problem with it.
- Frost Build-Up: In cold conditions, some frost is normal due to the Joule-Thomson effect when propane expands. However, excessive ice build-up may suggest a problem such as a leaking diaphragm or moisture inside the unit.
- Shut-Off Mechanism: Test the emergency shut-off mechanism to ensure that it completely stops the flow of propane when engaged.
- Professional Inspection: If you’re uncertain about its condition or if it’s due for a routine check, have a professional technician inspect it. They can perform a pressure drop test and other diagnostics to evaluate the health of the unit.
If your observations and tests raise any concerns about the functionality of the unit, it’s important to address these issues promptly. A malfunctioning unit can pose significant risks, so maintenance or replacement should be carried out by qualified personnel to ensure safe and efficient forklift operation.
What should you do if your propane regulator stops working?
If it stops working, you should check the following:
- First, check the propane tank to see if it is empty. If it is, then you will need to refill it.
- Next, check the connections between the propane tank and the regulator. Make sure that they are tight and secure.
- If the problem persists, you may need to contact a technician because there could be other issues in the fuel system.
Common issues can impact the efficiency and safety of the forklift’s operation. Regular maintenance and prompt troubleshooting are crucial in preventing and addressing these issues.
A. Regular Maintenance Requirements
- Visual Inspections: Conduct regular checks for physical damage, corrosion, or wear and tear.
- Leak Tests: Use soapy water or specific leak-detection solutions to identify any gas leaks, especially at connections and fittings.
- Pressure Checks: Verify that the unit is maintaining proper pressure levels according to manufacturer specifications.
- Cleaning: Remove dirt, debris, and oil that can accumulate on it.
- Replacement: Follow the manufacturer’s guidelines on the lifespan and replace it when necessary or if it shows signs of malfunction.
B. Troubleshooting Common Problems
- Propane Leaks
- Check for damaged seals, hoses, or connections.
- Tighten fittings and replace damaged parts as needed.
- Ensure proper installation of it and associated components.
- Inconsistent Pressure Output
- Inspect the diaphragm for damage or deterioration that may affect its responsiveness.
- Check for spring fatigue or failure that can affect pressure control.
- Verify that the vent is clear and not obstructed, as blockages can lead to pressure fluctuations.
- Frozen Regulator
- Ensure there is enough propane in the tank; low levels can cause moisture to freeze.
- Check for proper venting; a blocked vent can cause moisture build-up and freezing.
- Insulate the unit and lines in cold environments to prevent freezing.
- Contamination and Blockages
- Replace the filter if it is equipped with one, and check for any contamination in the propane supply.
- Clean out any debris or dirt that might be causing blockages.
- Regularly drain any accumulated oil or contaminants from if applicable.
C. Best Practices for Ensuring Long-Term Functionality
- Follow a Routine Maintenance Schedule: Adhere to the maintenance schedule recommended by the manufacturer.
- Use Quality Propane: Utilize clean, high-quality propane to minimize the risk of contamination.
- Train Operators: Ensure that operators are trained to recognize signs of the issues and understand proper start-up and shut-down procedures.
- Environmental Considerations: Install weather protection where necessary to protect the unit from extreme environmental conditions.
- Professional Assessments: Have the forklift and its fuel system assessed by a professional regularly to preemptively identify issues that may not be obvious to operators.
By following these guidelines for maintenance and troubleshooting, operators can greatly reduce the risk of regulator failure and prolong the life of the forklift’s propane fuel system. It is also critical to ensure compliance with all relevant safety standards and regulations.
Conclusion
In simple terms, think of a forklift propane regulator as a vital gadget that ensures your forklift runs well and safely. It’s like a control knob for the gas flow from the tank to the engine, making sure the gas pressure is just right for the engine to work its best.
Imagine the propane gas is like water in a hose with too much pressure. it calms this pressure down so your forklift can use it without a hitch. If it’s a two-part, it first eases the pressure a bit, and then in the second part, brings it down to a level that’s perfect for the engine. It’s smart too—it adjusts if the gas flow changes or if the tank pressure goes up or down, to keep the gas flow steady. Plus, it has built-in safety checks to stop the pressure from getting too high and causing trouble.
There are different styles for different forklifts, whether you need a simple setup or something more complex for bigger jobs or colder weather.
Just like you take your car for tune-ups, it’s important to regularly check the regulator for any leaks or wear and make sure it’s set right. When your unit is in good shape, your forklift works smoothly, doesn’t waste fuel, and keeps running costs down.
So, picking the right type, keeping it well-maintained, and fixing any problems quickly are all crucial for keeping your forklift in tip-top shape. This small piece of equipment has a big job and is key to a well-running propane forklift.
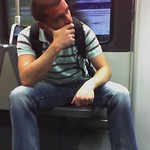
Mike is an experienced propane technician with over 15 years of professional experience in the field. He has dedicated his career to helping customers with their propane needs, from installation to maintenance and repair. Together with Jeremy, he co-founded this website to provide useful information and guidance to customers seeking reliable propane services.