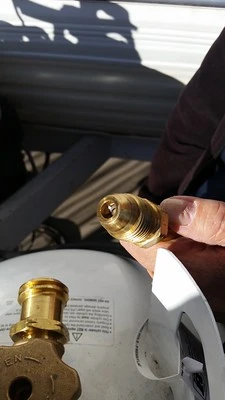
Propane regulator valves are critical components in propane systems, ensuring the safe and efficient delivery of gas from the tank to appliances. Problems with these valves can lead to issues with gas flow, affecting the performance of your propane-powered equipment. Here are some common problems associated with propane regulator valves and potential solutions:
1. Regulator Freezing
- Regulator freezing in propane systems is a phenomenon that occurs when the temperature of the propane gas drops sharply as it passes through the regulator, potentially causing moisture present in the gas to freeze. This effect is primarily due to the Joule-Thomson effect, which describes how a gas cools during expansion without external heat input. Propane, being compressed in the tank, expands and cools rapidly when it exits through the regulator, leading to a decrease in temperature. If there is moisture in the propane, this rapid cooling can cause the moisture to freeze, potentially blocking the regulator and affecting its operation.
- Symptoms of Freezing:
- A visible layer of frost or ice on the regulator or connecting hoses.
- Decreased gas flow to appliances, manifesting as lower flame heights or inability to sustain a flame.
- Complete blockage of gas flow in severe cases, rendering connected appliances inoperative.
- Potential Risks:
- Safety hazards due to inconsistent appliance operation.
- Damage to the regulator or appliance components from overpressure or due to attempts to manually remove ice.
- In extreme cases, the risk of gas leakage if the regulator or associated components are damaged by ice.
- Immediate Solutions:
- Safely thaw the regulator by stopping the gas flow and allowing it to come to ambient temperature naturally. Avoid using open flames or direct heat sources to accelerate thawing, as this poses a significant safety risk.
- Ensure that the gas tank is not overfilled, as excess moisture can exacerbate freezing issues.
- Preventive Measures:
- Moisture Reduction: Use a gas dryer or moisture trap in the system to reduce the moisture content of the propane before it reaches the regulator.
- Proper Installation: Ensure that the regulator is installed with the vent pointing downwards to prevent moisture from accumulating within the device.
- Insulation: Apply thermal insulation or use a regulator cover to keep the regulator’s temperature above the freezing point of water, reducing the likelihood of moisture freezing.
- Regular Maintenance: Schedule regular checks for signs of moisture or damage that could lead to freezing, ensuring the system is in optimal operating condition.
- Tank Positioning: In colder climates, consider the placement of the propane tank. Underground tanks or tanks placed in areas shielded from the wind can have less exposure to extreme cold, reducing the risk of regulator freezing.
2. Inconsistent Gas Flow
Causes
- Faulty Pressure Settings: Propane regulators are designed to reduce the tank’s high pressure to a usable level, typically around 11 inches water column (WC) (approximately 0.4 psi) for home appliances. Incorrectly adjusted regulators can result in too high or too low pressure, leading to inconsistent gas flow.
- Debris: Dirt, rust, or other particles can enter the regulator through the propane supply, causing obstructions that affect gas flow. These particulates can interfere with the regulator’s internal mechanisms, preventing it from properly modulating the gas pressure.
How to Diagnose and Verify
- Visual Inspection: Check for visible signs of damage or debris in and around the regulator and gas lines.
- Pressure Measurement:
- Use a manometer or pressure gauge to measure the gas pressure at the appliance end. For residential propane systems, the pressure should be around 11 inches WC. Deviations from this range can indicate a problem.
- To test the regulator’s function, you can measure the pressure both before and after the regulator. The pressure before (tank pressure) is typically much higher, around 100-200 psi, depending on the tank’s temperature and fill level. After the regulator, it should reduce to the appliance’s required pressure (e.g., 11 inches WC).
- Flow Rate Check: Inconsistent flow can also be diagnosed by checking the flow rate at the appliance. This requires specific flow measurement tools that can compare the actual flow rate to the appliance’s specifications.
Remedial Actions
- Adjusting Pressure Settings: If the pressure is found to be outside the specified range for your appliances, adjust the regulator following the manufacturer’s instructions. This often involves turning a screw on the regulator to increase or decrease the gas flow.
- Note: When adjusting the regulator, small increments are recommended. After each adjustment, use the manometer to measure and confirm the pressure setting is correct.
- Cleaning or Replacing the Regulator: If debris is suspected to be the cause of inconsistent flow:
- Disassemble and Clean: Some regulators can be carefully disassembled for cleaning. Remove any visible debris and inspect for damage. However, this should only be attempted if you’re familiar with the device and follow safety protocols.
- Replacement: In many cases, particularly with sealed units or when damage is detected, replacement of the regulator is the safest and most effective solution.
- Professional Inspection: If adjusting the pressure does not resolve the issue, or if there’s uncertainty about the system’s condition, consult a professional. A certified technician can perform a comprehensive inspection, including leak tests, pressure tests, and flow rate assessments, to identify and resolve the issue.
Key Measurements and Considerations
- Pressure Levels: Knowing the required pressure level for your appliances (typically 11 inches WC) and the normal tank pressure range is crucial for diagnostics.
- Safety Precautions: Always ensure gas is turned off before attempting adjustments or maintenance on the regulator or gas lines.
- Regulator Specifications: Refer to the regulator’s manual for specific adjustment instructions and operational parameters.
3. Gas Leak
Causes
- Damaged Diaphragm: The diaphragm in a propane regulator is a flexible membrane that responds to changes in gas pressure, ensuring a consistent flow rate. Over time or due to manufacturing defects, this diaphragm can become damaged, leading to a gas leak. Typical pressures regulated by these diaphragms range from the tank’s high pressure (100-200 psi) down to the appliance’s required pressure (about 11 inches water column or 0.4 psi).
- Improper Connections: Connections between the gas tank, regulator, and appliances that are not properly sealed can also lead to leaks. These connections are critical points where gas is transferred under pressure and require careful installation and maintenance.
Detection Methods
- Soapy Water Test: A simple and effective method for detecting gas leaks. Mix a soap solution (1 part dish soap to 1 part water) and apply it to the connections and along the hose. Bubbles forming indicate a leak. This method is sensitive enough to detect leaks that may not be noticeable by smell or other means.
- Electronic Gas Detectors: For a more thorough inspection, electronic gas detectors can be used. These devices can detect propane concentrations at very low levels, often parts per million (ppm), providing a precise indication of the presence of gas.
Corrective Measures
- For Damaged Diaphragms:
- Replacement: If the regulator’s diaphragm is damaged, the entire regulator typically needs to be replaced. Regulators are calibrated devices, and disassembly or repair by non-professionals can lead to safety hazards.
- Pressure Testing: After replacement, perform a pressure test using a manometer to ensure the regulator is correctly installed and operating at the proper pressure (e.g., 11 inches WC for home appliances).
- For Improper Connections:
- Tightening: If the leak is due to a loose connection, carefully tighten the connection with the appropriate tools. Avoid over-tightening, which can damage the threads or fittings, leading to further leaks.
- Replacing Seals: If seals or gaskets are damaged or worn, replace them with the correct type and size for your system. Ensure all connections are clean before reassembly.
- Professional Inspection: If you’re unsure about the source of the leak or how to repair it, or if the leak persists after your corrective actions, seek professional help. A certified technician can safely perform repairs and ensure your system is leak-free.
Key Measurements and Considerations
- Pressure Settings: Be aware of the specific pressure requirements for your appliances and ensure the regulator is adjusted accordingly.
- Leak Detection Sensitivity: The soapy water test can detect leaks at the bubble formation rate, while electronic detectors can specify the concentration in ppm, providing insight into the leak’s severity.
- Safety Precautions: Always shut off the gas supply before attempting any repairs. Work in a well-ventilated area to avoid gas buildup and potential health risks.
4. Low Gas Pressure
Reasons
- Blockage: Blockages in the regulator or gas lines can restrict gas flow, leading to low pressure. Common sources of blockage include dirt, debris, or ice formations, especially in the regulator’s vent or the gas lines themselves.
- Incorrect Adjustment: The regulator’s pressure setting may be incorrectly adjusted, providing less than the required pressure for proper appliance operation. Most home appliances require a gas pressure of about 11 inches water column (WC) or approximately 0.4 psi.
Impact on Appliance Performance
- Incomplete Combustion: Appliances receiving insufficient gas pressure can experience incomplete combustion, leading to soot formation and the emission of carbon monoxide, a hazardous gas.
- Reduced Efficiency: Low gas pressure results in lower flame heights and reduced heat output, making heating appliances less efficient and increasing the time required to cook or heat spaces.
- Appliance Malfunction: Some appliances have safety features that detect when gas pressure is too low, automatically shutting off the appliance to prevent unsafe operation.
Steps for Correction
- Identify the Cause:
- Visual Inspection: Check for visible signs of blockage in the regulator vent or gas lines. Look for frost buildup (indicating freezing) or debris.
- Pressure Check: Use a manometer to measure the gas pressure at the appliance end and at the regulator output. If the pressure is below the required 11 inches WC for appliances, there’s likely an issue with the regulator setting or a blockage in the system.
- Correcting Blockage:
- Clearing the Vent: Carefully clean the regulator vent, removing any debris or ice that may be causing a blockage.
- Inspecting Gas Lines: Ensure there are no kinks, bends, or physical obstructions in the gas lines that could restrict flow.
- Adjusting the Regulator:
- Adjustment Procedure: If the pressure is too low, adjust the regulator according to the manufacturer’s instructions. This usually involves turning an adjustment screw on the regulator to increase the pressure.
- Verification: After adjusting, re-measure the pressure with the manometer to ensure it meets the required 11 inches WC for proper appliance operation.
- Professional Assistance:
- If after attempting adjustments, the pressure remains low or you’re unable to identify the cause, seek professional help. A certified technician can perform a comprehensive system check, including leak tests and flow measurements, to diagnose and correct the issue safely.
Key Measurements and Considerations
- Pressure Requirements: Be aware of the specific pressure needs of your appliances. While 11 inches WC is standard for many home appliances, individual requirements may vary.
- Safety Precautions: Always ensure the gas is turned off before attempting any repairs or adjustments to avoid the risk of gas leaks or exposure.
- Regulator Compatibility: Ensure the regulator is correctly sized and rated for the flow and pressure requirements of your propane system. Using an undersized or improperly rated regulator can lead to chronic low pressure issues.
5. High Gas Pressure
Potential Causes
- Regulator Failure: The most common cause of high gas pressure is failure or malfunction of the propane regulator. Regulators are designed to reduce and maintain gas pressure from the tank (typically 100-200 psi) to a safe and usable level for appliances (around 11 inches water column or WC, equivalent to about 0.4 psi). A failure within the regulator’s mechanism can cause it to stop reducing the tank’s high pressure effectively.
Risks Associated with High Gas Pressure
- Appliance Damage: Appliances designed to operate at standard propane pressures (11 inches WC) can be damaged by higher pressures, leading to leaks, malfunctions, or complete failure.
- Safety Hazards: Excessive pressure may result in gas leaks at connection points, hoses, or appliance valves, increasing the risk of fire or explosion.
- Inefficient Combustion: High pressure can cause a richer gas mixture than appliances are designed to burn, leading to incomplete combustion, production of carbon monoxide, and soot accumulation.
Adjustment and Replacement Guidance
- Diagnosing High Pressure:
- Use a manometer to measure the gas pressure at the appliance or at a test point close to the regulator. If readings significantly exceed 11 inches WC, the regulator may be failing.
- Inspect the regulator for visible signs of damage or malfunction, such as hissing sounds, which can indicate internal failure or leakage.
- Regulator Adjustment (if applicable):
- Some regulators allow for manual adjustment. However, this should only be attempted if you are confident in your ability to accurately set the pressure and have the correct tools. Turn the adjustment screw slightly counterclockwise to reduce pressure, then re-measure.
- Caution: Improper adjustment can further increase pressure or damage the regulator. If unsure, proceed directly to professional evaluation.
- Regulator Replacement:
- If adjustment does not correct the issue, or if the regulator is damaged, replacement is necessary.
- Selection: Ensure the replacement regulator matches the specifications required for your system, including inlet pressure range, outlet pressure (11 inches WC for most home applications), and flow capacity in British Thermal Units (BTUs) per hour.
- Professional Installation: Given the risks associated with high gas pressure, consider hiring a certified technician for regulator replacement to ensure correct installation and pressure setting.
- System Check Post-Replacement:
- After replacing the regulator, use a manometer to verify that the outlet pressure is correctly set to the appliance’s requirements.
- Check all connections with a soapy water solution to ensure there are no leaks.
Key Measurements and Considerations
- Pressure Levels: Knowing the required pressure level (11 inches WC) and the normal operating pressure range of your tank and system is critical for diagnosing issues.
- Safety First: High gas pressure issues should be addressed with caution. If in doubt, shut off the gas supply and consult a professional.
- Regular Maintenance: Periodic checks of the gas pressure and regulator condition can help identify potential issues before they become serious problems.
6. Regulator Noise
Causes
- Oscillation: Noise can be caused by the oscillation of gas through the regulator, which occurs when the flow of gas causes internal components, like the diaphragm, to vibrate at audible frequencies. This is often related to the flow rate and pressure settings, where certain configurations can induce resonance within the regulator.
- Mechanical Vibrations: External or internal mechanical vibrations can also lead to noise. Externally, vibrations from connected appliances or piping can transmit through the system, causing the regulator to emit sound. Internally, worn or loose components within the regulator, such as springs or the diaphragm, can vibrate under the pressure of gas flow, generating noise.
Troubleshooting Tips
- Identify the Type of Noise:
- Listen to determine if the noise is a humming, whistling, or chattering sound. Humming or whistling is often related to gas flow, whereas chattering might indicate mechanical issues.
- Check Gas Flow and Pressure Settings:
- Ensure the regulator and gas system are configured correctly for the required flow rate and pressure. Misconfiguration can lead to oscillation noises. Use a manometer to verify that the pressure is set to the standard operating level for your appliances (typically around 11 inches water column or WC).
- Inspect for Loose Components:
- Check the regulator and surrounding connections for any loose parts or fittings that could be causing or contributing to the noise. Tighten any loose connections to ensure they are secure.
- Evaluate the Regulator’s Condition:
- Look for signs of wear, damage, or corrosion on the regulator. A damaged regulator may not function properly and could produce noise as a symptom of its failure.
- Reduce External Vibrations:
- If external vibrations are suspected, inspect the installation of the gas lines and regulator. Ensure they are securely mounted and that there is minimal contact with surfaces that could transmit vibrations.
- Adjust the Regulator or Flow Rate:
- If possible, slightly adjusting the regulator’s pressure setting or the flow rate can sometimes change the conditions causing the oscillation and eliminate the noise. This should be done cautiously to avoid affecting the performance of connected appliances.
- Replace the Regulator:
- If the noise persists despite troubleshooting and adjustments, the regulator may need to be replaced. Over time, wear and tear on internal components can lead to inefficiencies and noise that can only be resolved through replacement.
Key Considerations
- Safety: Always prioritize safety when inspecting and adjusting the propane system. Ensure the gas is turned off if you need to manipulate any components.
- Professional Assistance: If you’re unable to diagnose or resolve the noise issue on your own, it’s advisable to seek help from a professional. A certified technician can provide a thorough inspection and take appropriate corrective actions.
Conclusion
Addressing propane regulator valve problems is essential for the safety, efficiency, and reliability of any propane gas system. From regulator freezing caused by the Joule-Thomson effect to the risks associated with high gas pressure, understanding the underlying causes, potential risks, and appropriate corrective measures is crucial.
Whether it’s performing a simple soapy water test to detect leaks, adjusting pressure settings, or identifying the need for regulator replacement, each scenario requires careful consideration and a methodical approach.
Regular maintenance, including visual inspections and pressure checks, plays a vital role in preventing issues before they arise. However, when problems do occur, knowing how to troubleshoot and when to seek professional assistance can help mitigate risks and ensure your propane system operates smoothly.
Remember, safety should always be the top priority, and when in doubt, consulting with a certified professional is the best course of action to resolve propane regulator valve problems effectively.
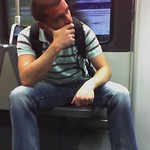
Mike is an experienced propane technician with over 15 years of professional experience in the field. He has dedicated his career to helping customers with their propane needs, from installation to maintenance and repair. Together with Jeremy, he co-founded this website to provide useful information and guidance to customers seeking reliable propane services.