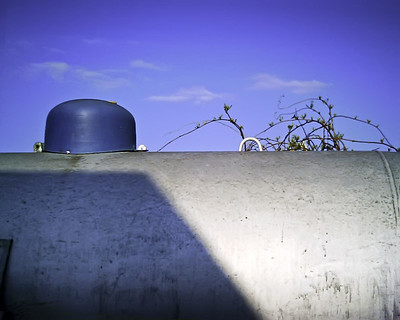
Propane is an incredibly versatile fuel used widely across homes, businesses, and industrial sites. Its safe and efficient storage is an essential consideration, especially for those relying on large quantities of this valuable fuel. This is where 500-gallon propane tanks come into play. But what exactly are these large propane tanks made of?
If you’ve ever asked this question, you’re not alone. It’s a subject that attracts interest from both homeowners and industry professionals alike. This article will provide a comprehensive exploration into the materials that construct these robust and reliable storage units.
Understanding the composition and manufacturing process of 500-gallon propane tanks gives a fascinating insight into their durability, safety, and lifespan. So, whether you’re curious about the durability of your home heating system or an industry professional looking to learn more about propane storage, read on as we dissect the makeup of a 500-gallon propane tank.
Read related articles:
- 500-Gallon Underground Propane Tanks: Will You Consider This?
- Ways to Hide a 500-Gallon Propane Tank in Your Property
- How Much Does 500 Gallon Propane Tank Weigh?
Materials Used in Manufacturing Propane Tanks
When it comes to the production of propane tanks, especially those capable of holding 500 gallons, the choice of materials is crucial. These materials need to satisfy specific criteria such as strength, durability, and non-reactivity to ensure safe and long-lasting storage.
A. Materials commonly used in propane tank production
A variety of materials are utilized in the production of propane tanks. However, the most commonly used material is metal, due to its robustness and ability to withstand high pressure. Various components such as valves, fittings, and gauges might use different types of metals like brass, aluminum, or specific kinds of steel, depending on the part’s function and design requirements.
B. The primary material used: Steel
The primary material used in the construction of 500-gallon propane tanks is steel.
- Types of steel used: There are different types of steel used in propane tank manufacturing, but mild and stainless steel are the most common. Mild steel, also known as low carbon steel, is renowned for its strength and formability. On the other hand, stainless steel is valued for its exceptional corrosion resistance.
- Justification for steel’s use: The use of steel in propane tanks is attributed to its high strength and durability. Steel can withstand the high internal pressures of a propane tank and is resistant to punctures and other physical damages. In addition, steel does not react chemically with propane, which is essential for maintaining the tank’s integrity over its service life.
C. The role of protective coatings
While steel is a strong and durable material, it is susceptible to rust and corrosion, especially when exposed to the elements over extended periods. This necessitates the use of protective coatings.
- Introduction to galvanization and powder coating: Two common protective coating techniques used in propane tank manufacturing are galvanization and powder coating. Galvanization involves coating the steel surface with a layer of zinc to protect it from corrosion. Powder coating, on the other hand, is a process where a dry powder is applied to the steel surface, forming a protective layer when heated.
- Importance of these coatings in rust prevention and overall tank longevity: These coatings significantly enhance the corrosion resistance of the propane tank, shielding the steel from moisture and other corrosive elements. Consequently, they help maintain the tank’s structural integrity and extend its lifespan, making them crucial components in propane tank manufacturing.
Read related articles:
- Is 500 Gallon Propane Tank The Right Size for Your Home?
- Where Can You Buy Used 500 Gallon Propane Tank for Sale?
- 500 Gallon Propane Tank Dimension: Is This the Size You Need?
How Thick is the Steel on a 500-Gallon Propane Tank?
The steel thickness of a 500-gallon propane tank’s shell is typically around 0.218 inches. It’s important to note that specific tank designs and manufacturers may have slight variations in the thickness, so it’s always recommended to consult the manufacturer’s specifications for accurate information regarding a particular tank model.
The shell thickness of 0.218 inches provides the necessary strength and structural integrity to withstand the pressure exerted by the propane stored inside the tank. This thickness is carefully determined to ensure the tank’s ability to withstand high-pressure conditions while maintaining safety standards.
The selection of the appropriate steel thickness is a critical aspect of propane tank design and manufacturing. It is based on various factors, including the intended usage, safety regulations, and engineering calculations. Tanks designed for higher pressures or specific applications may have different shell thicknesses to accommodate those requirements.
The steel used in the construction of propane tanks is typically high-quality, durable, and corrosion-resistant. It undergoes strict quality control measures to ensure it meets the necessary standards for propane storage. The thickness of the steel, along with other design features and safety components, contributes to the overall reliability and longevity of the tank.
It is important to note that the shell thickness alone does not determine the overall safety and performance of a propane tank. The tank’s design, manufacturing processes, and adherence to regulatory standards all play crucial roles in ensuring its safe operation. Therefore, it is essential to consult the manufacturer’s specifications and follow recommended guidelines for installation, usage, and maintenance to ensure the optimal performance and safety of a 500-gallon propane tank.
Anatomy of a 500-Gallon Propane Tank
A 500-gallon propane tank is not just a simple container for fuel; it is a meticulously engineered piece of equipment that balances function, safety, and longevity.
A. General structure and dimensions
A standard 500-gallon propane tank measures around 9.5 feet in length and 4 feet in diameter. It is usually designed as a horizontal cylindrical vessel. The tank is divided into two sections: the vapor space at the top, which houses gaseous propane, and the liquid space below, filled with propane in liquid form.
Given their size, these tanks are typically used in commercial settings, farms, or homes with high propane consumption. They are often installed above ground but can be placed underground if local regulations and safety measures allow.
B. Key features such as valves, gauges, and fittings
The 500-gallon propane tank is equipped with several key features to ensure safe and efficient operation. These include:
- Fill Valve: This is where propane is introduced into the tank during refilling.
- Service Valve: This is where propane gas exits the tank to be used in the home or business.
- Fixed Liquid Level Gauge: This indicates when the tank is filled to 80%, the maximum safe fill level to allow for propane expansion.
- Float Gauge: This provides a reading of the propane level in the tank at any given time.
- Pressure Relief Valve: This crucial safety feature allows pressure to be released from the tank if it becomes too high, preventing potential damage or rupture.
- Bleeder Valve: This is used during the filling process to ensure the tank is not overfilled.
C. Importance of materials used for safety and longevity
500-gallon propane tanks are primarily made of steel, a material chosen for its strength, durability, and resistance to damage. The tank’s body is usually made of thick, high-grade steel to withstand the pressurized propane inside. Additionally, steel is advantageous because it does not react with propane, reducing the risk of corrosion from within the tank.
To protect against external threats, the outer surface of the tank is often treated with special coatings. Galvanization or powder coating provides an extra layer of resistance against rust and corrosion, extending the lifespan of the tank.
The materials used in 500-gallon propane tanks play a critical role in their safety and longevity. Through a combination of robust steel construction and protective surface treatments, these tanks are designed to securely store propane and withstand environmental conditions for many years.
Production Process of 500-Gallon Propane Tanks
The manufacturing process of 500-gallon propane tanks is a complex procedure involving a series of stages to ensure the final product is safe, durable, and able to hold and distribute propane effectively.
A. The manufacturing process
The production process generally begins with designing and cutting the steel to be used for the tank. Once cut, the steel plates are shaped and welded to form the body of the tank. After the initial assembly, fittings, valves, and gauges are installed. Then, the tank undergoes a series of tests to ensure its safety and durability. Finally, protective coatings are applied to prevent corrosion and prolong the tank’s lifespan.
B. The role of steel in the shaping and welding stages
Steel plays a critical role in the manufacturing process, especially during the shaping and welding stages. Steel plates are initially cut into appropriate sizes before being molded into a cylindrical shape to form the body of the tank. Welding is then used to join these pieces together, creating a sealed environment for the propane. The strength and durability of steel make it the ideal material for this process, as it can withstand the heat from welding and the subsequent high pressures of stored propane.
C. Application of protective coatings
Once the welding and assembly of the tank are complete, protective coatings are applied to the outer surface of the tank. As mentioned earlier, the most common coatings are galvanization and powder coating. The application of these coatings is a critical step in the manufacturing process as they provide the tank with enhanced resistance against rust and corrosion, which can compromise the tank’s integrity over time.
D. Quality control and safety testing
Quality control and safety testing are crucial steps in the production process of 500-gallon propane tanks. Tanks are typically pressure tested to ensure they can safely hold propane under normal and extreme conditions. They are also inspected for any manufacturing defects, such as inadequate welds or improperly installed fittings. Only tanks that pass these rigorous safety tests and meet the necessary standards are deemed fit for use.
The production process of a 500-gallon propane tank involves careful material selection, precise assembly, thorough testing, and the application of protective measures. These stages collectively ensure the finished product is safe, robust, and ready for many years of service.
Regulations and Standards for Propane Tanks
For the safe operation and use of propane tanks, there are numerous regulations and standards in place. These guidelines ensure tanks are manufactured to stringent safety requirements, thus protecting users and the environment.
A. Overview of key regulations and standards
Several regulatory bodies set guidelines and standards for propane tanks, including the National Fire Protection Association (NFPA), the American Society of Mechanical Engineers (ASME), and the Department of Transportation (DOT). These organizations mandate the design, manufacturing, installation, and operation of propane tanks.
NFPA 58, also known as the Liquefied Petroleum Gas Code, is a key standard that provides comprehensive safety requirements for all aspects of propane handling, including storage tank manufacturing.
ASME sets the standards for pressure vessel design, which includes propane tanks, ensuring they can safely handle the high pressures associated with storing propane.
DOT regulations focus on the transportation of propane and the design of portable tanks meant for transport.
B. Impact of these standards on material selection and tank construction
The regulations and standards set by these bodies directly influence the materials used and the construction methods in propane tank production.
For example, ASME pressure vessel standards dictate specific grades and thicknesses of steel for use in propane tanks, as these materials have been tested and proven to safely withstand high pressures.
Similarly, NFPA 58 influences the design and features of the tank, such as required safety valves and gauges, as well as guidelines for tank installation and use.
C. Compliance testing and certification process
To ensure adherence to these standards, propane tanks undergo extensive compliance testing throughout the manufacturing process. Tests include pressure tests, leak tests, and structural integrity tests. Tanks are also inspected for correct installation of all features, including valves, gauges, and protective coatings.
Once a tank passes all required tests and inspections, it is certified as compliant with the relevant standards. This certification process is essential for guaranteeing the safety and quality of each propane tank, providing users with confidence in their propane storage solution.
To Make a Conclusion
Understanding what 500-gallon propane tanks are made of is essential for anyone using or considering propane as an energy source. These tanks are carefully constructed to ensure the safe and efficient storage of propane, providing a reliable fuel supply for residential, commercial, and industrial applications.
The primary material used in the manufacturing of 500-gallon propane tanks is steel, known for its strength, durability, and resistance to high pressures. Different types of steel, such as mild and stainless steel, may be utilized based on specific design requirements. The steel undergoes shaping, welding, and assembly processes to create the tank’s structure, while protective coatings like galvanization and powder coating are applied to enhance its resistance to rust and corrosion.
Compliance with regulations and standards set by organizations such as NFPA, ASME, and DOT ensures that propane tanks meet stringent safety requirements. These standards influence material selection, tank construction, and the inclusion of safety features like valves, gauges, and protective coatings.
The production process of 500-gallon propane tanks involves meticulous quality control and safety testing to ensure their reliability. Tanks are tested for pressure, leaks, and structural integrity to guarantee safe operation. Certification is obtained upon successful compliance with the standards.
By understanding the materials and manufacturing processes involved in the construction of 500-gallon propane tanks, users can appreciate their durability, safety, and longevity. It is crucial to consult manufacturer specifications, follow recommended guidelines, and prioritize proper installation and maintenance practices to ensure the optimal performance and safety of these tanks.
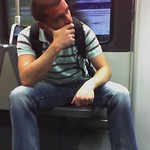
Mike is an experienced propane technician with over 15 years of professional experience in the field. He has dedicated his career to helping customers with their propane needs, from installation to maintenance and repair. Together with Jeremy, he co-founded this website to provide useful information and guidance to customers seeking reliable propane services.