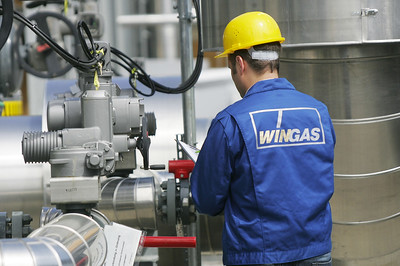
The question of whether a natural gas line can be used for propane is an important topic to consider when exploring fuel options for residential or commercial applications. Natural gas and propane are both widely used as energy sources, but they have distinct properties that require specific equipment and components for safe and efficient operation.
This article will discuss the key differences between natural gas and propane, the reasons why it is generally not recommended to use a natural gas line for propane without proper conversion, and the steps necessary to safely switch between these two fuel sources.
By understanding the risks and requirements associated with each gas type, users can make informed decisions about their energy needs and ensure the safe operation of their appliances and systems.
It Is Generally Not Recommended Because of These Reasons
It is generally not recommended to use a natural gas line for propane without modifications, as natural gas and propane have different properties and require different components for safe and efficient operation. Here are a few reasons why:
- Pressure difference: Propane is usually supplied at a higher pressure than natural gas, which means that propane appliances require different pressure regulators.
- Orifice size: The orifice size for propane burners is smaller than that for natural gas burners, as propane has a higher energy content per unit volume. Using a natural gas orifice with propane can result in too much fuel being released, causing an oversized flame and potentially dangerous conditions.
- Gas control valves: Propane and natural gas have different specific gravities, and the control valves used for each gas type are designed to work optimally with the respective gas.
- Safety concerns: Using propane in a natural gas line without proper conversion can lead to incomplete combustion, carbon monoxide buildup, and an increased risk of fire or explosion.
- Density and Dispersion: Propane is heavier than air and will pool in low-lying areas, while natural gas (methane) is lighter than air and will rise. If there’s a leak in a system initially designed for natural gas, propane won’t dissipate as quickly, leading to an increased risk of explosion or fire.
- Corrosiveness: The specific materials used in natural gas lines might not be resistant to propane, which can lead to corrosion over time.
- Energy Content: Propane has a higher energy content than natural gas. Using propane in a system designed for the BTU output of natural gas can result in over-firing appliances.
- Regulatory and Code Implications: In many jurisdictions, using a natural gas line for propane might violate local building codes or regulations, which can result in fines or legal implications.
If you want to switch from natural gas to propane or vice versa, you should consult with a licensed professional to determine if your system can be safely converted. This will typically involve changing the orifices, pressure regulators, and potentially some other components to ensure compatibility with the new fuel source.
The Pressure is Different
You are correct that natural gas pipelines have compressor stations at intervals of approximately 50-100 km to maintain the pressure and flow of gas through the pipeline network. These compressor stations are specifically designed to handle gaseous natural gas and not liquids.
Propane, on the other hand, can exist in both liquid and gaseous states, depending on the temperature and pressure conditions. When propane is subjected to the typical working pressures of 12-100 kg/cm², it can become a liquid. Using the natural gas pipeline infrastructure for transporting propane could present a significant challenge, as the compressors at the recompression stations are not designed to handle liquids.
Introducing propane in its liquid state into a pipeline system meant for gaseous natural gas could lead to malfunctions and damage to the compressors, as well as potential safety hazards. Therefore, it is crucial to maintain separate infrastructure for transporting natural gas and propane to ensure the safe and efficient functioning of the pipeline networks.
Safety Implications
Expansion and Contraction Properties of Both Gases | |
---|---|
Natural Gas |
Comprised mostly of methane, it tends to expand and contract moderately with temperature changes. The effect of expansion can influence the pressure inside a pipeline, especially if the pipeline is not adequately ventilated or regulated. |
Propane |
Exhibits more significant expansion and contraction with temperature fluctuations. Requires a robust pressure regulation system to ensure safe operation, given its expansive properties. |
Leak Detection and the Importance of Odorants | |
Natural Gas |
In its pure form, natural gas is odorless. An odorant, usually mercaptan, is added to give it a distinct ‘rotten egg’ smell, aiding in leak detection. Its lighter-than-air property means it will disperse upward when leaked, reducing ground-level concentration. Still, accumulation in closed spaces can pose an explosion risk. |
Propane |
Also odorless in its natural state, propane too has an odorant added for safety reasons. Unlike natural gas, propane is heavier than air. If leaked, it can pool at ground level, increasing the risk of ignition if not detected. |
Combustion Characteristics: Flame Temperature and Ignition Point | |
Natural Gas |
Ignition temperature: Around 1,000 to 1,200°F (538 to 649°C). Flame temperature in air: Approximately 3,600°F (1,982°C). |
Propane |
Ignition temperature: Roughly 920 to 1,120°F (493 to 604°C). Flame temperature in air: Close to 3,595°F (1,979°C). |
Regulatory Implications
Regulatory and Code Implications | |
---|---|
Overview of Regulations Guiding Gas Line Installations |
Many countries and states have specific regulatory bodies that dictate the standards for gas line installations. Regulations often address design, construction, operation, maintenance, and safety aspects. |
Differences in Codes for Propane and Natural Gas Installations |
Natural Gas: – Pipelines may have specific material and design requirements due to the gas’s corrosive nature. – Due to its expansive nature, there might be strict regulations concerning ventilation and pressure regulation. Propane: – Given propane’s propensity to pool at ground level, codes might emphasize proper ventilation at low points. – Storage tanks and systems often have specific requirements to accommodate propane’s unique properties. |
Implications of Converting or Using a Gas Line for a Fuel it Wasn’t Originally Intended For |
– Potential for equipment malfunction or decreased lifespan due to differences in gas properties. – There could be legal or insurance implications for not adhering to specified fuel use. – Safety risks associated with incorrect pressure regulation or inadequate leak detection. – Possible voiding of warranties or certifications for equipment and installations. – It’s vital for consumers and professionals to be fully aware of these safety and regulatory implications when considering conversions or modifications to existing gas line systems. |
Let’s Explore the Differences to Know The Reasons Why Natural Gas Lines Be Used for Propane
Natural gas and propane are two common fuel sources used in residential, commercial, and industrial applications. Both of these energy sources provide clean and efficient options for heating, cooking, and powering various appliances. However, understanding the differences between natural gas and propane systems is essential to ensure the safe and efficient operation of equipment. This article will delve into the properties of natural gas and propane, the key differences in components and infrastructure, safety concerns, and the process of converting between the two fuel sources.
Properties of Natural Gas and Propane
Natural gas primarily consists of methane, while propane is a separate hydrocarbon with its own distinct properties. The energy content of propane is higher than that of natural gas on a per-unit volume basis, which means that appliances using propane generally require smaller orifices for fuel delivery. Additionally, propane is typically supplied at a higher pressure than natural gas, necessitating the use of different pressure regulators.
Another important consideration is that propane can exist in both liquid and gaseous states depending on temperature and pressure conditions. In contrast, natural gas remains in a gaseous state under normal pipeline operating conditions.
Key Differences in Components and Infrastructure
The differences in properties between natural gas and propane necessitate the use of specific components and infrastructure designed for each fuel type. Pressure regulators must be matched to the appropriate fuel source, as propane requires higher pressure regulation than natural gas. Similarly, orifice sizes for burners must be tailored to the fuel, with propane burners having smaller orifices than their natural gas counterparts.
Gas control valves are also designed to work optimally with specific fuel types, considering the differences in specific gravities between natural gas and propane. Furthermore, pipeline infrastructure and compressor stations for natural gas are tailored to accommodate the gaseous state of the fuel. Introducing propane, which can exist as a liquid under certain conditions, into a pipeline designed for natural gas could lead to malfunctions, damage to compressors, and potential safety hazards.
Gas Piping and Pressure are So Much Different
The pressure in residential gas lines is relatively low, typically ranging from 0.25 psi (pounds per square inch) to 0.5 psi for natural gas and around 11 inches of water column (approximately 0.4 psi) for propane. The gas supply system is designed to provide the required amount of gas to each appliance based on their specific needs.
Gas piping is sized to accommodate the combined demand of all connected appliances. When a new appliance is added to the system, it is important to ensure that the existing gas line can handle the additional load without affecting the performance of the other appliances. If the gas line is undersized or not properly designed, the appliances may not receive the necessary amount of gas, causing them to operate inefficiently or not at all.
Starvation of gas can lead to several issues, such as reduced performance, improper combustion, and an increased risk of carbon monoxide buildup. When adding a new appliance to a gas system, it is crucial to consult with a licensed professional to assess the gas line capacity and make any necessary modifications. This may include upgrading the gas line size, adjusting pressure regulators, or installing additional gas lines to ensure that all appliances receive an adequate supply of gas without compromising safety or performance.
What Kind of Fittings for Natural Gas
When installing or modifying natural gas systems, it is essential to use the appropriate fittings to ensure a safe and secure connection. There are several types of fittings commonly used for natural gas lines, including:
- Black iron pipe fittings: Black iron pipe fittings are one of the most common types of fittings used in natural gas systems. They are made of malleable iron and coated with a black finish to protect against corrosion. They are strong, durable, and suitable for low-pressure applications like residential and commercial natural gas installations. Examples of black iron pipe fittings include elbows, tees, couplings, unions, reducers, and caps.
- Brass fittings: Brass fittings are corrosion-resistant and suitable for use in natural gas systems. They are often used in conjunction with copper tubing, particularly for indoor applications. Brass fittings include adapters, connectors, elbows, tees, and valves.
- Flare fittings: Flare fittings are used with flexible metal tubing, like copper or stainless steel, and provide a secure, leak-proof connection. They work by using a flared end on the tubing that fits into a corresponding flare fitting. When the nut is tightened, it compresses the flared tubing against the fitting, creating a tight seal. Flare fittings are commonly used for connecting gas appliances to the gas supply line.
- Compression fittings: Compression fittings work by compressing a metal or plastic ferrule onto the tubing, creating a tight seal. They are often used for connections involving flexible gas lines, such as corrugated stainless steel tubing (CSST). However, they are generally not recommended for black iron pipe or other rigid gas lines.
- Quick-connect fittings are designed for easy installation and disconnection, often used for portable gas appliances like outdoor grills or patio heaters. They typically consist of a male and female coupling that connects securely when pushed together.
It is important to consult local building codes and regulations, as well as the manufacturer’s guidelines for the specific gas system and appliances being installed, to ensure that the appropriate fittings are used. Working with a licensed professional can help ensure that the gas system is safely installed and properly maintained.
Difference Between Natural Gas and Propane Fittings
While natural gas and propane fittings might look similar, there are some differences that must be considered when working with these two fuel types. The primary differences stem from the fact that propane and natural gas have different properties, such as energy content, pressure requirements, and specific gravity. This means that fittings for each fuel type may have differences in design, materials, and pressure ratings to ensure safe and efficient operation.
Here are some key differences between natural gas and propane fittings:
- Pressure ratings: Propane is typically supplied at a higher pressure than natural gas. As a result, propane fittings and components may have higher pressure ratings to accommodate the increased pressure requirements.
- Material compatibility: Although both natural gas and propane fittings are often made of similar materials, such as brass, black iron, and stainless steel, there may be subtle differences in the materials’ composition or coatings to ensure compatibility with the specific fuel type.
- Thread types: While both natural gas and propane fittings generally use standard National Pipe Thread (NPT) connections, some specialized propane fittings may utilize different thread types, such as the left-hand thread (reverse thread) found in some propane cylinder connections. These reverse threads are used as a safety measure to prevent accidentally connecting a propane cylinder to a natural gas appliance or vice versa.
- Appliance-specific fittings: Gas appliances designed for propane use may have different connection fittings than those designed for natural gas. For example, propane regulators, hoses, and connectors may not be directly compatible with natural gas systems.
- Quick-connect fittings: Some quick-connect fittings for propane and natural gas systems may look similar but are designed specifically for each fuel type. Connecting the wrong type of quick-connect fitting to an appliance can lead to leaks, improper fuel flow, or unsafe operation.
Converting between Natural Gas and Propane Systems
Converting between natural gas and propane systems is a process that may be necessary when changing the fuel source for appliances or equipment in residential, commercial, or industrial settings. To ensure the safe and efficient operation of these systems, it is essential to follow proper conversion procedures and consult with licensed professionals.
Professional consultation and assessment: The first step in the conversion process is to consult with a licensed professional, such as a heating, ventilation, and air conditioning (HVAC) technician or a plumber experienced in gas systems. These professionals can assess the compatibility of the existing system with the new fuel source and determine the necessary modifications.
Necessary modifications to components and equipment: Converting between natural gas and propane typically involves changing several components of the system. Some of the primary modifications include:
- Pressure regulators: Since propane is supplied at a higher pressure than natural gas, the pressure regulator must be replaced or adjusted to accommodate the new fuel source.
- Gas control valves: The gas control valves must be replaced or adjusted to work optimally with the specific gravity of the new fuel.
- Pilot lights and ignition systems: Some appliances may require adjustments or modifications to the pilot light or ignition system to ensure proper combustion with the new fuel source.
- Ensuring safe operation and compliance with regulations: After the necessary modifications have been made, the professional will test the system to ensure that it operates safely and efficiently with the new fuel source. This may involve checking for gas leaks, ensuring proper combustion, and verifying that the system complies with local regulations and safety standards. See NFPA code.
- Maintenance and ongoing support: Regular maintenance and inspections are important to ensure the continued safe operation of the converted system. This may include annual inspections by a licensed professional, as well as routine maintenance tasks, such as checking for gas leaks, cleaning burners, and ensuring proper venting.
Conclusion
Natural gas and propane, though commonly used as household and industrial fuels, possess distinct physical and chemical characteristics. Some of the key differences include their composition (methane for natural gas and propane for the latter), their densities, and their energy content. These differences manifest in various practical implications, particularly when considering the suitability of infrastructure and appliances for each gas type. The pressure at which propane is stored, its propensity to pool in low areas, and its higher energy content compared to natural gas make using natural gas lines for propane potentially hazardous.
It cannot be stressed enough that the direct use or conversion of systems between these two gases isn’t a straightforward task. Given the intricacies and the risks involved, any considerations for conversion or dual-purpose use should be approached with caution. Always prioritize safety and compliance with local regulations. It is paramount to seek the expertise of professionals in the field when contemplating such changes, ensuring the safety and efficiency of the system and adhering to all pertinent safety standards and regulations.
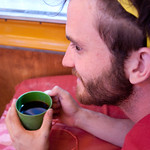
Jeremy is a highly experienced professional propane technician with over 21 years of experience in the industry. Throughout his career, he has gained extensive knowledge and expertise in propane gas installation, maintenance, and repair, as well as in ensuring safety and compliance with industry standards. Mike has worked with various residential, commercial, and industrial clients, providing top-notch services and solutions to meet their propane needs. He is dedicated to his craft and passionate about delivering exceptional service to his clients.