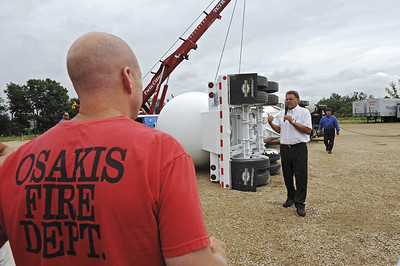
Propane is an incredibly versatile and valuable energy source, widely used across a range of industries, from agriculture to construction, and even in our own homes.
However, just as with any fuel, handling and storing propane safely is of utmost importance. Proper training is essential not only for meeting legal requirements but also for ensuring the well-being of your employees and protecting your business from potential accidents.
In this guide, we’ll walk you through the steps of developing and implementing an effective propane safety training program for your employees.
We’ll explore various training methods, tips for ensuring effective learning, and the importance of keeping your training up-to-date. So, let’s dive in and discover how to create a safer work environment for everyone, one propane safety lesson at a time!
Identifying the Need for Training
Before you begin designing your propane safety training program, it’s important to assess your work environment and determine the training needs specific to your organization.
Assessing the work environment
Take a close look at the areas where propane is used or stored in your workplace. Identify potential hazards, such as leaks, improper storage, and insufficient ventilation. These findings will help you understand the risks your employees face and the specific training they’ll need to address those risks.
Identifying employees who handle propane
Make a list of all employees who come into contact with propane in their daily work, whether they handle the fuel directly or work in proximity to propane equipment. These employees will require targeted training to ensure their safety.
Determining training requirements based on roles and responsibilities
Different employees will have different levels of responsibility when it comes to propane safety. For example, managers may need to be trained in implementing safety policies and procedures, while maintenance staff may need more technical knowledge about inspecting and repairing propane equipment. Tailor your training program to suit the specific needs of each employee group.
Developing a Comprehensive Propane Safety Training Program
Once you’ve identified your organization’s training needs, it’s time to develop a propane safety training program that covers all the essential topics.
A. Setting clear objectives and goals
Begin by outlining the primary objectives of your training program. What do you want your employees to learn? What skills should they acquire? Having clear goals will help you design a training program that meets the specific needs of your organization.
B. Covering essential topics
Your propane safety training program should cover the following key topics:
Properties of propane
- Physical and chemical properties
- Combustion and flammability characteristics
- Hazards associated with propane use
Propane handling and storage
- Safe handling practices
- Proper storage techniques
- Transportation and transfer procedures
Safety equipment and personal protective equipment (PPE)
- Types of safety equipment used in propane handling
- Proper use and maintenance of PPE
- Selection criteria for PPE
Emergency procedures
- Emergency response plans
- First aid for propane exposure
- Firefighting techniques and equipment for propane fires
Preventive maintenance and inspections
- Regular inspection schedules
- Identifying signs of wear and damage
- Maintenance and repair protocols
C. Customizing training to suit specific industries and workplaces
Every industry and workplace has unique characteristics and hazards related to propane use. Customize your training program to address these specific needs, ensuring that your employees receive relevant, practical training.
Choosing the Right Training Method
There are several different methods of delivering propane safety training, each with its own advantages and disadvantages. Consider your organization’s needs and resources when selecting the right method for your employees.
A. In-person training
In-person training, led by a qualified instructor, is a traditional and effective method of teaching propane safety. This approach allows for direct interaction between the instructor and the employees, as well as opportunities for hands-on practice.
Pros and cons
- Pros: Direct interaction, immediate feedback, hands-on practice, and easy adaptation to specific workplace situations
- Cons: Can be more expensive and time-consuming, requires scheduling and coordinating sessions, and may be less flexible in terms of timing and pace
Choosing a qualified instructor
Select an instructor with a strong background in propane safety and industry-specific knowledge. Look for certifications, experience, and references to ensure you’re choosing a reliable and effective trainer.
B. Online training
Online training is a convenient and flexible option, allowing employees to learn at their own pace and on their own schedule. This method is particularly useful for organizations with remote workers or multiple locations.
Pros and cons
- Pros: Cost-effective, flexible scheduling, self-paced learning, and easy access to training materials
- Cons: Limited opportunities for hands-on practice, reduced interaction with instructors, and potential technology barriers for some employees
Selecting a reliable online training provider
Choose a reputable online training provider with a proven track record in propane safety training. Look for user reviews, accreditation, and industry-specific content to ensure you’re getting a quality training program.
C. Blended learning approach
A blended learning approach combines the benefits of both in-person and online training. This method allows employees to complete some portions of the training online at their own pace, while still participating in hands-on, in-person sessions for more practical components.
Combining in-person and online elements
Identify which aspects of your propane safety training program would benefit most from in-person instruction, such as hands-on practice and equipment demonstrations. Use online training for more theoretical components, like learning about the properties of propane and emergency procedures.
Tailoring the blend to fit the organization’s needs
Adjust the balance of in-person and online training to suit your organization’s specific needs, resources, and employee preferences. This may involve using more online training for remote workers, while still providing in-person sessions for employees who require hands-on practice.
Ensuring Effective Training
To get the most out of your propane safety training program, make sure it’s engaging, interactive, and encourages employee participation.
Utilizing interactive learning techniques
Incorporate interactive learning techniques into your training program, such as group discussions, case studies, and role-playing exercises. These methods help to increase employee engagement and reinforce learning.
Encouraging employee participation
Invite employees to ask questions, share their experiences, and contribute to the learning process. This promotes a sense of ownership and commitment to propane safety, increasing the likelihood that employees will apply their newfound knowledge in the workplace.
Providing opportunities for hands-on practice
Whenever possible, offer employees opportunities to practice what they’ve learned in a controlled environment. This not only helps to reinforce learning but also builds confidence in handling propane safely.
Evaluating and assessing employee understanding
Regularly assess your employees’ understanding of propane safety concepts through quizzes, tests, and practical demonstrations. This will help you identify any gaps in their knowledge and make adjustments to your training program as needed.
Maintaining and Updating Propane Safety Training
Propane safety training is not a one-time event. To keep your employees well-prepared, it’s important to review and update your training materials regularly and provide refresher courses as needed.
Regularly reviewing and updating training materials
Stay informed about the latest industry standards, regulations, and best practices. Use this information to update your training materials and ensure that your employees receive the most up-to-date and relevant information.
Providing refresher training courses
Schedule periodic refresher courses to reinforce key concepts and keep employees’ knowledge fresh. This is particularly important for employees who do not handle propane on a daily basis, as they may be more prone to forgetting essential safety procedures.
Staying up-to-date with industry standards and regulations
Regularly review and stay informed about changes in industry standards, regulations, and best practices. This will help you maintain a proactive approach to propane safety and ensure that your employees are always trained in accordance with the latest guidelines.
Decide Whether to Conduct It Onsite or At an Offsite Training Facility
When deciding whether to conduct propane safety training onsite or at an offsite training facility, it’s important to consider the unique needs, resources, and circumstances of your organization.
Each option has its own advantages and disadvantages, and choosing the right one will depend on factors such as your workplace setup, the size of your employee group, and your organization’s specific training objectives.
Onsite Training:
Pros:
- Convenience: Conducting training at your workplace can save time and reduce the logistical challenges of transporting employees to an offsite facility.
- Familiarity: Employees will learn safety procedures in the actual environment where they’ll be handling propane, making the training more relevant and practical.
- Customization: Onsite training allows for the training program to be tailored specifically to your workplace and its unique hazards, ensuring that employees are well-prepared for the specific challenges they may face.
- Cost-effectiveness: By conducting training onsite, you may save on expenses associated with renting a training facility and transportation costs for your employees.
Cons:
- Distractions: Onsite training may be subject to interruptions and distractions, which can impact the effectiveness of the training.
- Space constraints: Depending on the size of your workplace, you may have limited space for training activities, particularly those involving hands-on practice.
Offsite Training Facility:
Pros:
- Dedicated environment: A training facility is specifically designed for educational purposes, often featuring appropriate equipment, materials, and resources for a comprehensive propane safety training experience.
- Fewer distractions: Offsite training can provide a more focused learning environment, free from the distractions and interruptions of the workplace.
- Networking opportunities: Attending training at an offsite facility may offer employees the chance to network with peers from other organizations, fostering valuable connections and opportunities for learning from others’ experiences.
Cons:
- Cost: Renting a training facility and arranging transportation for employees can be more expensive than conducting training onsite.
- Less customization: Offsite training may be less tailored to your specific workplace, as the training environment may not perfectly mimic your employees’ actual work setting.
The choice between onsite and offsite propane safety training will depend on your organization’s specific needs and circumstances. Consider factors such as your budget, the size of your employee group, the relevance of the training environment, and the potential for distractions when making your decision.
You may even find that a combination of both onsite and offsite training is the best solution for your organization, providing a well-rounded and comprehensive propane safety training experience.
You Can Hire a Consultant to Determine the Best for Your Requirement
Hiring a consultant to determine the best propane safety training program for your specific requirements can be a wise investment for your organization. A consultant can provide valuable insights and expertise in the field of propane safety, ensuring that your training program is tailored to meet the unique needs of your workplace and employees.
The benefits of hiring a consultant for your propane safety training needs include:
- Expert knowledge: Consultants typically have extensive experience in propane safety and are well-versed in industry standards, regulations, and best practices. They can provide expert guidance on creating a comprehensive training program that covers all essential aspects of propane safety.
- Customized approach: A consultant can help you develop a training program that is specifically designed to address the unique risks and hazards present in your workplace. This ensures that your employees receive relevant, practical training that is directly applicable to their daily tasks.
- Objective perspective: An external consultant can offer an unbiased viewpoint on your organization’s propane safety needs, helping you identify areas for improvement that may have been overlooked internally. This fresh perspective can lead to a more effective and targeted training program.
- Time and resource savings: Developing and implementing a propane safety training program can be a time-consuming and resource-intensive process. By hiring a consultant, you can leverage their expertise and experience to create a more efficient and effective training program, saving both time and resources.
- Ongoing support: Many consultants provide ongoing support and guidance after the initial training program has been implemented. This can include regular updates on industry regulations, refresher courses for employees, and assistance with addressing any propane safety issues that may arise.
- Improved workplace safety: Ultimately, working with a consultant can lead to a safer work environment for your employees. By providing high-quality, targeted training, your employees will be better equipped to handle propane safely and prevent accidents related to propane use and storage.
Hiring a consultant to determine the best propane safety training program for your specific requirements can be a valuable investment in your organization’s safety and overall success. By leveraging the expertise and experience of a consultant, you can ensure that your employees receive the most relevant, effective, and up-to-date training possible, ultimately creating a safer workplace for everyone involved.
Conclusion
Investing in propane safety training is a crucial step towards creating a safer work environment for your employees and protecting your business from potential accidents. By following the steps outlined in this comprehensive guide, you’ll be well on your way to developing and implementing an effective propane safety training program tailored to the unique needs of your organization.
Remember, a well-trained workforce is not only more productive but also more confident and secure in their daily tasks. As an employer, it’s your responsibility to promote workplace safety and provide your employees with the tools and knowledge they need to handle propane safely.
Don’t wait until it’s too late – start planning your propane safety training program today and enjoy the peace of mind that comes with knowing your employees are well-prepared to handle this valuable but potentially dangerous energy source.
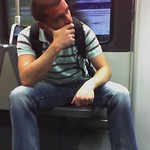
Mike is an experienced propane technician with over 15 years of professional experience in the field. He has dedicated his career to helping customers with their propane needs, from installation to maintenance and repair. Together with Jeremy, he co-founded this website to provide useful information and guidance to customers seeking reliable propane services.